Carbon-Free Technology: Implications for Aluminum
by Dr. Subodh Das, Phinix, LLC
18th Annual Jacobs Consultancy Petcoke Conference
San Antonio, Texas
March 9, 2019
Several alternative aluminum smelting technologies have evolved over the years to reduce the amount of energy consumption and GHG emissions during the Hall-Heroult process. The industry has been doing research and development on this technology for more than a century and several patents have been awarded to organizations and individuals.
One of the key technologies that have been able to gain notable achievements in reducing carbon emission per ton of aluminum production is a combination of Inert anode and Carbon Cathode. Download the paper “Carbon-Free Technology: Implications for Aluminum” presented by Dr. Subodh Das, Phinix, LLC.
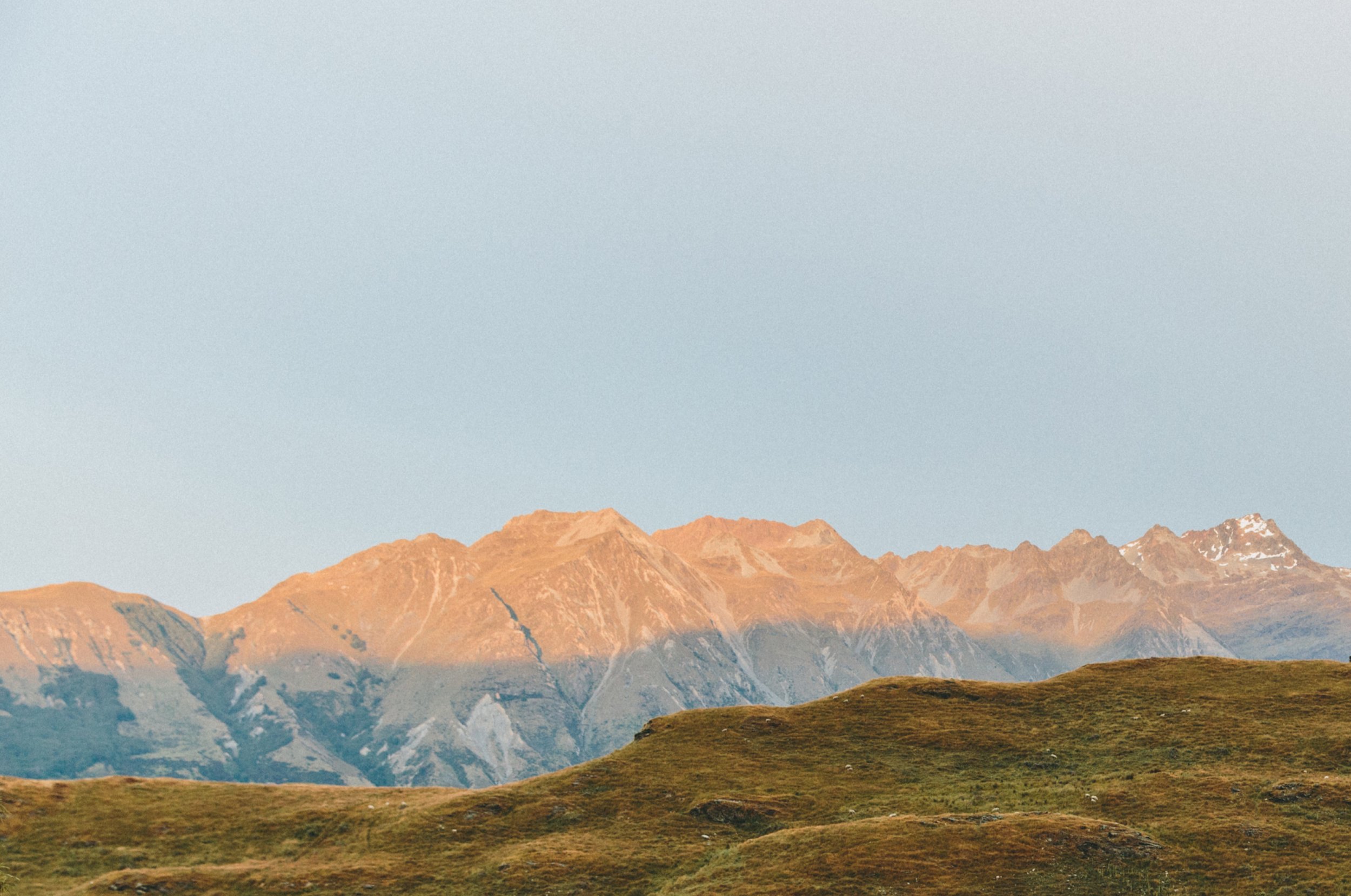
Current Status and Proposed Economic Incentives for Higher Utilization of Bauxite Residue to Enhance Sustainability of the Aluminum Industry
The Neglected Areas of Aluminum Sustainability: Mitigation of Bauxite Residue (Red Mud)
Aluminum and the sustainability dilemma
Aluminum exists in the earth’s crust in its oxidized form as bauxite ore, which contains over 35% concentration of aluminum hydroxide. Aluminum is extracted from the bauxite rock in a complicated three-stage production process.
Aluminum has been dubbed a “green metal” for its recycling possibilities and its lightweighting capacities. On the other hand, the extraction process of the metal is extremely energy intensive, which causes greenhouse gas emissions and generates large volumes of hazardous byproducts. This is the dichotomy that has posed serious barriers to the industry majors in achieving the sustainability goals that have been outlined by the Paris Agreement and the Circular Economy framework.
The aluminum production process
In the three-stage production process of aluminum, bauxite is first mined from the earth and then refined into alumina, which is then reduced to aluminum through an electrolytic process. Bauxite is refined into alumina through the Bayer Process, which is the sole industrial alumina production process across the world. Subsequently, alumina is transformed into molten aluminum metal through the Hall-Héroult process. As a rule of thumb, about four tons of bauxite are required to produce two tons of alumina which can produce one ton of aluminum.
Sustainability challenges across the value chain
The three-stage production chain of aluminum from ore to casting is complex and consumes huge amounts of energy and input materials. The process requires 13,000 to 18,000 kWh/t of electric energy under the best- and worst-case scenarios[i]. And an average of 12 kgs of CO2eq is emitted per kg of aluminum smelting worldwide[ii]. This process also results in undesirable by-products, including bauxite tailings, bauxite residue, dross, spent pot lining, etc. Here is an illustration of the range of sustainability challenges aluminum faces across the value chain:
(Published in Light Metal Age, The Quest for Low Carbon Aluminum: Developing a Sustainability Index, 2021)
Since electricity generation and consumption and GHG emission remains the two key interrelated challenges in this energy intensive industry, the concept of aluminum sustainability has so far been zoomed into CO2eq emission and the fuel that is used to generate electricity.
This article throws light on a neglected area of sustainability – bauxite residue management – which can pose serious environmental and health hazards and have a detrimental impact on aluminum’s sustainability roadmap.
Bauxite residue needs immediate attention
Bauxite residue is a waste product produced during the extraction of alumina from bauxite through the Bayer process. Rich in iron and aluminum components, the composition of bauxite residue depends on the source and the extraction process.
Bauxite residue generation can vary from 0.3 to 2.5 tons per ton of alumina produced, depending on the quality of bauxite and extraction conditions, though typically, it lies between 1 and 1.5 tons. Before disposal, bauxite residue is washed to extract as much caustic soda and dissolved alumina as possible. After washing, the residue is disposed of in special facilities known as Bauxite Residue Disposal Areas (BRDA) or Residue Storage Areas (RSA). The usual practice allows storing bauxite residue in slurry form, but some alumina producers also practice dry disposal.
The stockpile and the risk
As per a 2018 estimate, globally, the aluminum industry generates more than 150 million tons of bauxite residue annually and there exists a global inventory of more than 3 billion tons.
Metallurgical alumina production is forecasted to increase from 140 million tons in 20122 to 178 million tons by 2040. With the growing production of alumina, bauxite residue generation is likely to increase significantly. According to the International Aluminium Institute’s dynamic material flow model, bauxite residue production is likely to reach about 160 million tons per year in 2020 and 10 billion tons by 2050.
High alkalinity and high caustic content in bauxite residue cause environmental risk for fertile soil and groundwater contamination. The caustic (NaOH) content in bauxite residue leads to human health risks. Moreover, disposal of bauxite residue requires a large area, which means loss of huge land and soil, which could otherwise be used for green cover or other vegetation. There have been instances in the past when the bauxite residue slurry got released into the surrounding environment and residential areas due to leakage in the red mud ponds causing loss and injury of life along with damaging soil and waterbodies.
Bauxite residue management: Industry practice
From this huge stockpile of bauxite residue that gets generated every year, only about 2.5 to 5 million tonnes get recycled every year. About 3 million tonnes are utilized every year in the production of Portland Clinker Cement, according to IAI data. This is by far the most widely known use of bauxite residue globally. Other than that, bauxite residues are also used for:
· Brick production
· Soil improvement
· Landfill covering
· Iron production
These are just experimental uses so far and the valorized volume is much lesser than the generated stockpile. The industry has not yet been able to find an environmentally and commercially viable solution for bauxite residue valorization.
Case studies of bauxite residue valorization
India’s Hindalco, a part of the Aditya Birla Group, was the world’s 1st company to undertake a 100% red mud utilization strategy in 2020. The company signed an agreement with UltraTech Cement, India’s largest cement manufacturer, to deliver 1.2 million tons of bauxite residue per year to be used as input materials.
UAE’s EGA has begun constructing a pilot plant to convert bauxite residue into soil products that can be used for greening and other purposes in the UAE.
Further, Hydro Alunorte recently signed a contract with Wave Aluminium to build a plant in Brazil to process bauxite residue, aiming to recover commercially valuable materials. The planned processing plant aims to process 50,000 tonnes of bauxite residue per year. The technology has been tried and tested on a laboratory scale.
Currently, three aluminum companies in three countries: Ukraine, Greece, and India currently, process bauxite successfully, as per International Aluminium Institute data:
Country Company Maximum usage (t)
Ukraine Mykolayviv 250,000
Greece Mytilineos 85,000
India Hindalco 2,000,000
Proposal for a bauxite residue premium
One of the biggest bottlenecks in valorizing bauxite residue within a market economy is economic viability. There is no dearth of technological options to manage bauxite residue. However, any given utilization pathway will only be pursued if it is economically viable along with being environmentally beneficial. Hence, the initiatives need the policymaker’s support or monetary incentive.
In the green aluminum field, producers are already exploring a premium pricing structure for low-carbon aluminum, primarily based on electricity sourced from hydropower. Very few aluminum producers get access to hydropower and no new hydro dams are under construction for environmental reasons. The hydro-based premium does not apply to most global aluminum production. Hence, producers enjoying the benefits of a low-carbon aluminum premium already have the advantage of cheaper hydropower. Further, this is creating a barrier between green and black aluminum, driving coal-powered aluminum producers toward the sustainability roadmap.
This calls for a new pricing premium for London Metal Exchange (LME) traded primary P1020 aluminum designed to incentivize the effective utilization of newly produced and existing bauxite residue. A producer can claim a higher premium for the removal of problematic existing bauxite residue compared to a newly produced lot. The bauxite residue mitigation premiums will apply equitably to all primary aluminum producers using any fuel source. A premium based on higher bauxite residue utilization will encourage producers to churn out primary aluminum adhering to low-bauxite residue requirements. This could be a disruptive proposal. However, it can be a workable solution to deal with the necessary problem in the aluminum industry, needing an urgent and disruptive approach.
[ii] “Greenhouse Gases from Major Industrial Sources”; Ref no PH3/23 by ICF Consulting USA
DOE Funds Next-Generation Rare Earths Processing Research Collaboration with Phinix, LLC and Virginia Tech
Urban mining and Landfill Mining are two terms that are used interchangeably to represent the extraction and processing of wastes from landfills. However, urban mining is a broader concept compared with landfill mining.
Urban Mining and its Potential: In Relation to Aluminum Recover
Urban mining and Landfill Mining are two terms that are used interchangeably to represent the extraction and processing of wastes from landfills. However, urban mining is a broader concept compared with landfill mining.
E-Waste: The Flip Side of Digital Mobility
About 53.6 million tons (Mt) of e-waste was generated worldwide in 2019, up 21% in just five years, according to the UN’s Global E-waste Monitor 2020. The volume is likely to touch 74.7 million tons (Mt) by 2030 – almost doubling in only 16 years.
Magnesium Production: China Crisis and Growing Opportunity For ROW
Magnesium is one of the most strategic materials in modern engineering and manufacturing of aluminum alloys. The significance of the metal lies in its ability to offer weight reduction in critical components without compromising on strength. The key applications of magnesium are in the fields of automotive, aerospace, medical and electronic, the automotive taking about 62% of its share. The lightweight impact of Al and Mg alloys in transportation is well documented by the U.S. Department of Energy’s Vehicle Technology Office (USDOE-VTO). Global demand for magnesium has significantly increased over the past decade (CAGR 2001-2021 at 5.1%), owing to the unprecedented growth in sectors such as construction, automobiles, iron, and steel, etc.
Aluminium Recycling: Current Industry Benchmark and Circular Economy Potential
I’m glad to share with my connections that my article “Aluminium recycling: Current industry benchmark and circular economy potential” was published in the Aluminium International Today Magazine September/October 2021 issue. The article throws light on the potential of aluminum recycling in improving the circular economy credential of the aluminum industry. While doing so, it analyses the International Aluminium Institute’s material flow analysis for aluminum and touches upon the US aluminum recycling scenario.
The Recent Rally in Aluminum; How Different it is From the Commodity Boom in 2000’s
LME aluminum recently touched the $3,000/MT mark on September 13, not seen any time after 2008, when it registered the lifetime high of $3,292/MT. The aluminum price is about 50% up from the lows it saw in May 2020. The current rally in price is mostly driven by the fear of a supply crunch in China in a period of high demand. The price rise also brought about the fear of an impending correction to be followed soon. Are prices going to come down soon? I see no such indication.
Low Carbon Aluminum in Can Sheet Applications: A Marketing Gimmick or a Sustainable Trend?
Low carbon aluminum is the order of the day across the global aluminum industry. While it is taking shape as a marketable commodity with a designated premium across the global metal exchanges and in the financial market, several big-ticket end-use consumers have already unveiled their commitment towards carbon neutrality by vowing to use low carbon aluminum in their products.
Aluminum Sustainability As We See It: Whole Vs. Part
We all are aware of the parable of the blind men and an elephant that originated in India, from where it has been widely diffused and used in various contexts. The story shows how different perspectives, partial observation, and selective focus sometimes give a simpler picture of a more complex reality. In a nutshell, it is the conflict of whole vs. parts or integrated vs. individual.
Phinix LLC, Virginia Tech (lead), and Covanta Win Prestigious R&D contracts from the US Department of Energy, ARPA-E
Sustainable Resource management has been the key focus area for Phinix LLC, founded and headed by Dr. Subodh Das in 2008. The company has been delivering successful R&D projects for the light metal industry focusing on processes & product development, energy efficiency & conservation, recycling, scrap sortation & sustainability.
Phinix LLC and Partners win R&D project from US Department of Energy, EERE
Phinix LLC has added another R&D contract to its list of prestigious projects focusing on processes & product development, energy efficiency & conservation, recycling, scrap sortation & sustainability. The company has been awarded an R&D contract by the U.S. Department of Energy - Office of Energy Efficiency & Renewable Energy (EERE).
Remade Institute Awards Key PCB Recycling Technology Project to Virginia Tech and Phinix LLC
Remade Institute recently awarded a project contract to a research team comprising Virginia Polytechnic Institute and State University (lead) and Phinix LLC. The project is designed for recovering valuable materials from end-of-life printed circuit boards (PCB).
How serious are we about aluminum recycling?
With the exponentially growing aluminum demand, it is evident that there would not be enough primary aluminum available to meet the demand indefinitely.
Are we neglecting the serious sustainability issues across the aluminum value chain?
Are we neglecting the serious sustainability issues across the aluminum value chain while focusing exclusively on fuel sources? Using hydropower cannot be the only solution that can address the sustainability challenges in aluminum.
Sustainability in aluminium: CO2 emission and beyond
The threat of climate change, and the growing focus on a carbon-neutral world and the implementation of a circular economy has changed the way heavy industries operate now. The result was the Paris Agreement in 2016, which set up an aim of keeping global warming below 2 degrees Celsius over the 21st century.
This transformation is driving a series of much-needed changes in the product development process, technology, and the end-use of materials. Aluminium and a range of other metals are expected to play a key role in this transformation process.